Operation & Maintenance
Operation and maintenance are often discussed as one activity (i.e., O&M), but they are two, different, but interrelated, activities. How assets are operated will impact how assets need to be maintained and vice versa. Therefore, when the operations plan for an asset is developed, the maintenance plan also needs to be considered. However, the two activities usually do not happen at the same time — for example, an asset might be taken out of service for maintenance. Maintenance and operation are not always completed by the same personnel. It is imperative that the operations and maintenance personnel communicate regularly. Otherwise, it will be difficult to optimize or schedule maintenance so it causes the least disruption in operations.
Operations
The purpose of the operations phase is to ensure the asset is operated as it was intended, within design specifications, with maximum uptime until it reaches the end of its useful life. In this phase, operation activities are performed and tracked. The collection of data in this phase assists in decision making for all phases of the asset’s life.
Operations, or operational activities, can be classified into three categories:
- Standard operating procedures – Operations carried out routinely to ensure the system is performing as expected.
- Alternate operating procedures – Procedures used when the system is not being operated in a routine fashion. This might be due to maintenance or other activities that require it. For example, by-passing an asset.
- Emergency operating procedures – These plans are used in response to a specific event that poses an immediate risk to health, life, property, or the environment.
Personnel should be familiar with all three types of procedures, or they should know where they can find the procedures when needed in resources such as in a book, online, or in a shared site.
Asset operations can be passive or active. If an asset is passive, it does not require regular human interaction for it to do its job. These types of assets include categories such as pipe, storage tanks, utility access holes, and many green assets, including bioswales and pervious pavement. If an asset is active, it will need human interaction or control technology to start/stop it and adjust its operation to meet the conditions and requirements at the time. These types of assets include pumps, chlorinators, scrapers, and chemical addition systems.
There are also some assets that are both passive and active. An example would be an isolation valve in a water distribution system. The valve is normally in an open or closed position and functions as a passive asset since no intervention is required for it to stay in this position. However, if a major pipe break occurred, the valve would need to be closed with human intervention. In this case, the asset becomes an active asset.
These distinctions become most important in alternate and emergency operating procedures. Passive assets are unlikely to need any change in operation, while active assets or those that are a bit of both might require changes.
The system should have a plan in place that lays out the who, what, when, and how of the daily operations. It should define how resources (personnel, financial and physical) will be allocated to achieve the Level of Service goals. The operations plan is a manual for operating the system.
Maintenance
The purpose of the maintenance phase is to ensure the asset is fully functional and performs optimally until it reaches the end of its useful life. In this phase, all maintenance activities are performed and tracked. The collection of data in this phase assists in decision making for all phases of the asset’s life.
Maintenance involves those activities that help keep the assets in good working order, so they will operate as intended. Maintenance falls into the broad categories listed below. Different names or definitions of maintenance can be used, and systems might combine categories of maintenance in different ways than described below. The most important thing is to complete these types of maintenance, no matter what they are titled.
- Routine or Planned Maintenance – regularly scheduled maintenance, completed on a calendar or use base schedule (i.e. every month or every 1,000 hours of run time). This maintenance is outlined in a maintenance plan that includes required tasks, labor, materials, etc. This maintenance is based on a maintenance strategy such as predictive (monitor), preventive or run-to-failure in which case the corrective maintenance can still be planned.
- Predictive Maintenance – condition monitoring used to predict when asset failure is likely to occur. This maintenance might require equipment that the system might have to rent, purchase, or borrow, and it might require an outside contractor to complete. In some cases, predictive maintenance is easy and inexpensive. In others, it can be quite complex and costly. The cost will dictate how much and what type of predictive maintenance is reasonable, and risk will determine upon which assets predictive maintenance makes sense.
- Preventive Maintenance – conducted to maintain operating condition and slow deterioration. Completed based on condition and ability to provide Level of Service while the asset is still in working condition. Intended to prevent unexpected failures. Preventive maintenance should be scheduled to limit downtime.
- Warranty-Related Maintenance – maintenance required to keep warranty from being voided. This maintenance should be performed on the schedule and manner required by the warranty.
- Corrective/Reactive Maintenance – completed after an asset has failed. It is the result of an unexpected event, the lack of a maintenance strategy, or having the Run-to-Failure or Plan-to-Replace strategy in place. If reactive maintenance occurs on an asset that has a predictive (monitor) or preventive maintenance strategy in place, and the strategy indicated the asset was not expected to fail, it might be necessary to investigate whether the monitoring was insufficient or inaccurate, or the analysis of the monitoring data was incorrect. In these cases, the maintenance plan might need modification to address the problem.
- Backlog Maintenance – preventive maintenance that is not yet on the schedule. The backlog might be caused by seasonal activities or weather events. Keep the number of backlog activities to a reasonable number, so they can eventually be completed as part of planned maintenance and preferably within a year (unless the maintenance is on a longer-term than annual).
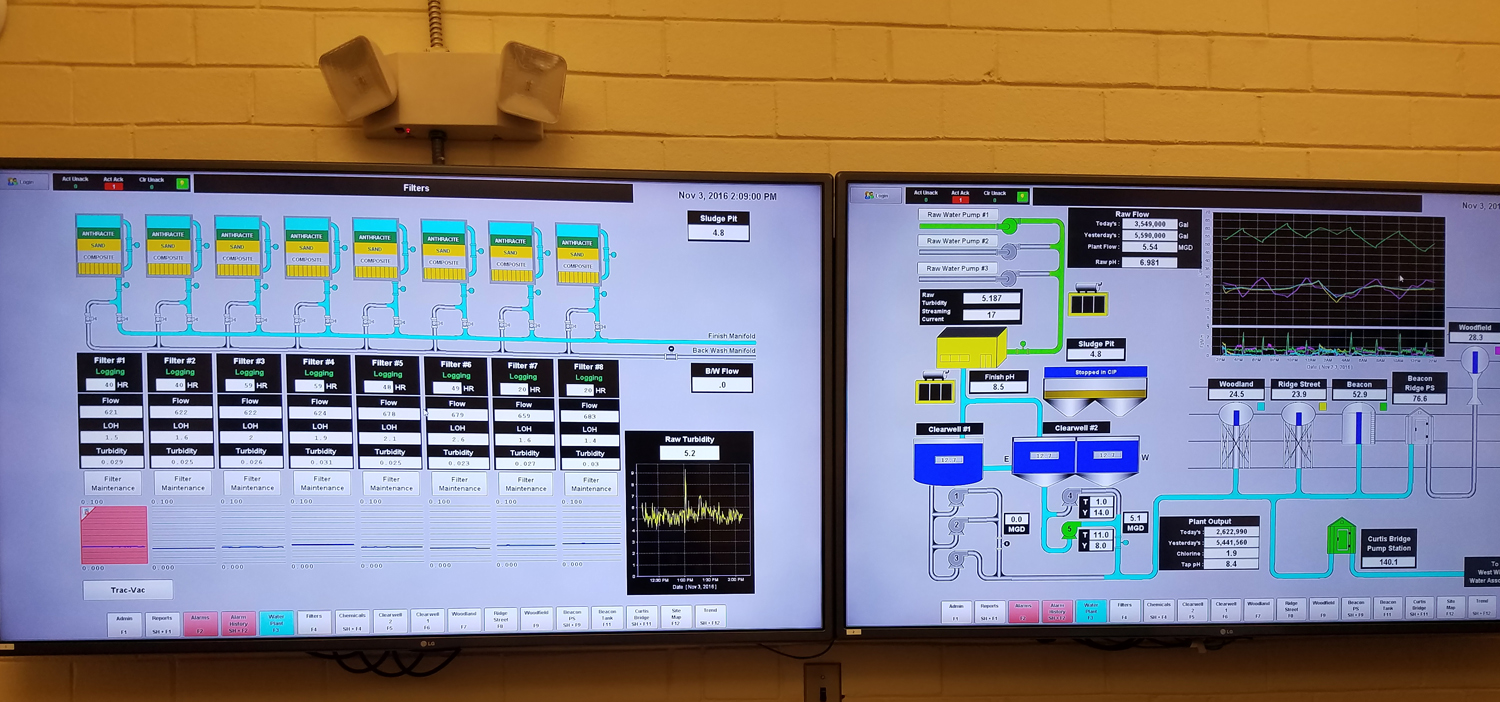
In most cases, maintenance activities should be expected. Even when failures occur, many of them are expected failures. For example, a part might be known to wear out on a certain schedule or due to certain kinds of events. Failures might also be known based on experience with similar assets. Maintenance can be completed when an asset fails (reactive) or can be completed before the asset fails (proactive). In some cases, the failure is unexpected, and the only option is reactive maintenance.
The type of maintenance completed and the maintenance schedule should be determined based on information regarding asset performance, monitoring information, and asset risk. When considering risk, higher risk assets will have more resource expenditures than lower risk assets. Properly maintaining an asset and investing in proactive maintenance for higher risk assets allows a system to spend its limited maintenance dollars as efficiently as possible. A well-operated and maintained asset is likely to have more up-time and a longer useful life.
A companion activity to maintenance is monitoring (which includes inspection). Use monitoring to help determine when maintenance should be performed. Monitoring can be on-going and permanent using continuous read equipment, or it can be intermittent. Monitoring might also allow the asset’s operation and maintenance to be adjusted and improved over time.
Maintenance is completed to maintain the asset’s condition. When maintenance is not completed as scheduled, or maintenance no longer allows the asset to meet the Level of Service required, additional, more costly efforts might be needed. For green assets that are intended to last indefinitely, proper maintenance should keep the asset from needing extensive efforts. However, even green assets might have components that need to be rehabilitated or replaced, such as individual plants or the soil due to contamination.
If assets are not well designed and operated (including passive assets), they might require more maintenance. This is one of the many reasons communication that includes operators and maintenance staff is so important during planning and design phases.
Data Collection
To know the optimal way to operate and maintain the asset, it is important to collect operational and maintenance data. Operational data should include items such as run time, uptime, and the costs to operate. Maintenance data should include the costs for any maintenance activities conducted. Both operational and maintenance data can aid informed decision-making. You can also use data to improve decision-making after failures. For information on Data Management click here.