Construction and Installation
The construction or installation phase is when the asset goes from existing only on paper to existing in reality. The scope of the project will determine the length and complexity of construction and the need for some of the possible steps listed below.
To move from the design phase to the construction phase, staff need to select a product supplier and/or construction contractor. If the scope of the project is large enough, the system will likely need to receive bids on the project. To do this, the system must develop a Request for Bids (RFBs). The Resources section has some tools to use in developing RFBsRequest for Bids.
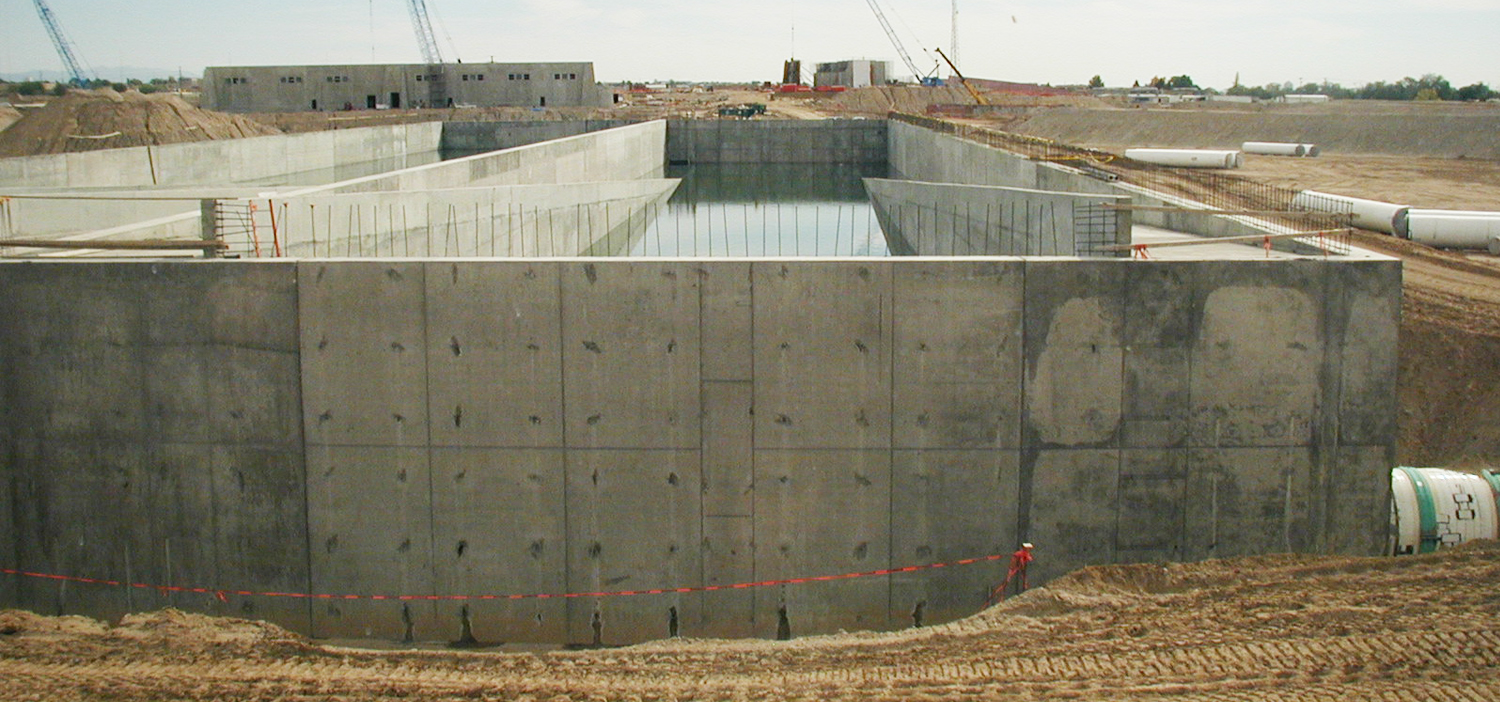
There are often standard construction or installation procedures developed for types of assets. These standards exist to ensure that similar assets are installed by each construction company the same way. They also help ensure assets installed by developers, especially those that will eventually be taken over by the system, are installed correctly. These types of standards are particularly important for green assets, as they are often installed by others. Pipe assets are another asset type that will likely have standard procedures.
Sometimes the standard procedures will need to be revised based on the installation conditions. The ability to revise standard installation procedures should be discussed with the engineer and the contractor before bids are received and during construction. For example, if the ground contains sharp rock, a trench might require 18 inches of bedding instead of the standard 6 inches.
Construction inspection should be completed for most construction projects to ensure the installation is going as planned. Even though the contractor and/or engineer has a construction inspector on-site, the system personnel should also visit the construction site as often as possible. This presence during construction can help ensure that construction proceeds according to plan, provide information to the operations staff of construction conditions, provide observations of buried assets, and correct any construction problems before they become permanent. Any time the contractor and/or engineer plan an inspection meeting, system staff should be advised and should participate in those meetings.
Testing the operation of the asset before final construction is something that might occur depending on the design and the construction contract. The system should be aware of the testing of any equipment and should participate in those events.
System staff should make sure construction is well documented. As-built drawings should be tracked daily and added to the system’s GISGeographic Information Systems map as part of the construction contract. It is important to make sure the as-built drawings accurately reflect what was installed. If possible, the drawings should be provided in an electronic format compatible with whatever software the system uses. The system should indicate that it will own the electronic files after the project is completed.
In addition to as-built drawings, system staff should request information on all the new assets added to the facility. This asset inventory should include all the attribute information desired and should be in a format compatible with the system’s electronic asset inventory. If the system does not yet have an electronic format, at the very least, the information should be provided in a standard format, such as a spreadsheet or .csv. This requirement needs to be included in either the construction contractor or engineer’s RFBRequest for Bid/RFPRequest for Proposal and the contract. It must also be clear that the system owns the data after the project.
Other documents that should be provided upon completion of construction include Operation and Maintenance Manuals, Standard Operating Procedures, Manufacturer’s Warranties and/or Contractor’s Guarantee. The system should always be able to access these documents. The warranties and guarantees should be examined carefully to see if there are any requirements for maintenance or operation to make sure the warranties remain valid. The system would not want to find out after the fact that failure to perform a particular task on a particular schedule resulted in voiding of the warranty. Often this type of work is called “warranty” work and can be specified as such in the work order system. In the case of warranty work, the system should not change any of the procedures or time frames to ensure warranties remain in effect.
The system might need to invest in operator training before or right after taking ownership of the assets. Lack of training or improper training can result in resentment, downtime or even employee injury. The contract should include adequate training for the operators and maintenance personnel. It is also worth considering the timing of the training. Often, training is provided only at the very beginning of operation. At this time, the situation is likely to be chaotic and activities might seem reasonable. However, after some time (perhaps weeks or a few months), the operators or maintenance personnel might have questions or concerns that could be addressed by additional training. It is suggested that training be done in phases with some at the beginning and additional training happening later in the process. If there is training available for green assets, splitting the training over time might even be more important. These assets can change over time as plants mature.